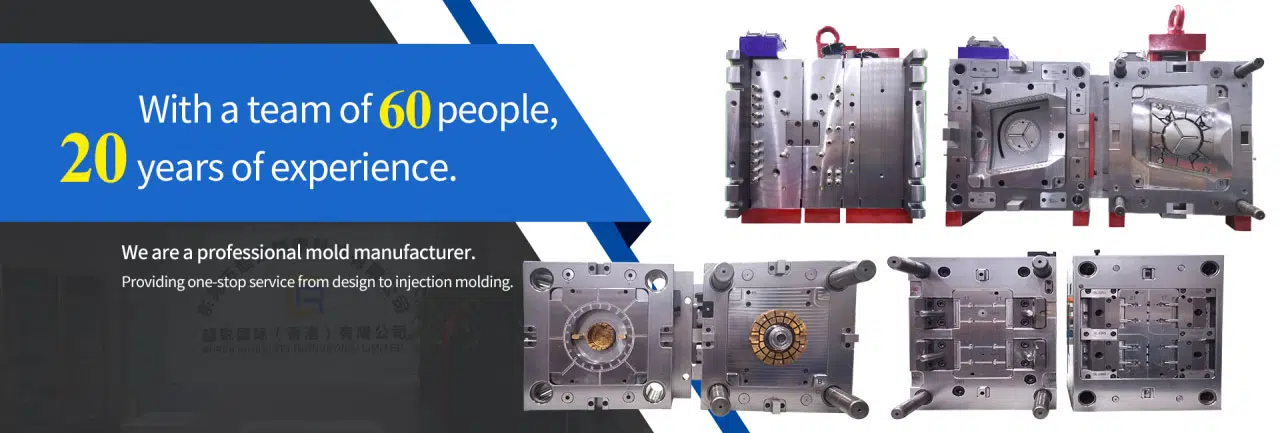
# High-Precision Machining Technology and Its Applications
## Introduction to High-Precision Machining
High-precision machining refers to the manufacturing process that achieves extremely tight tolerances and superior surface finishes. This advanced manufacturing technique plays a crucial role in industries where component accuracy is paramount, such as aerospace, medical devices, and electronics.
## Key Technologies in High-Precision Machining
Several technologies enable high-precision machining:
### 1. CNC Machining
Computer Numerical Control (CNC) machines provide the foundation for high-precision manufacturing. Modern CNC systems can achieve tolerances within microns through advanced control systems and feedback mechanisms.
### 2. Ultra-Precision Machining
This category includes processes like diamond turning, micro-milling, and precision grinding that can achieve sub-micron accuracy and nanometer-level surface finishes.
### 3. EDM (Electrical Discharge Machining)
EDM technology uses electrical sparks to remove material, allowing for intricate shapes and hard materials to be machined with high precision.
## Applications of High-Precision Machining
### Aerospace Components
The aerospace industry relies heavily on high-precision machining for critical components like turbine blades, fuel system parts, and structural elements that must withstand extreme conditions.
Keyword: High-Precision Machining
### Medical Devices
From surgical instruments to implants, high-precision machining ensures the reliability and safety of medical equipment. Components like orthopedic implants require exceptional accuracy for proper fit and function.
### Electronics Manufacturing
The production of semiconductors, connectors, and other electronic components demands machining capabilities at microscopic levels to meet the ever-shrinking size requirements of modern electronics.
## Challenges in High-Precision Machining
Despite its advantages, high-precision machining faces several challenges:
– Thermal deformation of materials during machining
– Tool wear and its impact on dimensional accuracy
– Vibration control at microscopic scales
– Cost-effectiveness for mass production
## Future Trends
The future of high-precision machining includes:
– Integration of AI for real-time process optimization
– Development of new materials with improved machinability
– Advancements in metrology for better quality control
– Miniaturization of machining systems for micro and nano applications
As technology continues to evolve, high-precision machining will play an increasingly vital role in manufacturing industries that demand the highest levels of accuracy and quality.