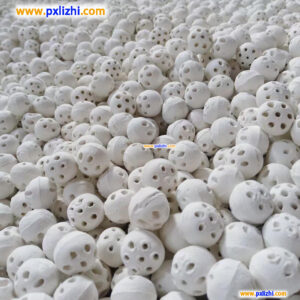
# Alumina Cerical Ball Applications and Properties
## Introduction to Alumina Ceramic Balls
Keyword: alumina ceramic ball
Alumina ceramic balls are high-performance ceramic spheres made from aluminum oxide (Al₂O₃). These precision-engineered components have become essential in various industrial applications due to their exceptional properties. With alumina content typically ranging from 90% to 99.9%, these ceramic balls offer superior performance compared to traditional metal alternatives.
## Key Properties of Alumina Ceramic Balls
### 1. Exceptional Hardness
Alumina ceramic balls rank 9 on the Mohs hardness scale, making them one of the hardest materials available for industrial applications. This property makes them highly resistant to wear and abrasion, significantly extending their service life in demanding environments.
### 2. High Temperature Resistance
These ceramic balls maintain their structural integrity at temperatures up to 1600°C (2912°F), making them ideal for high-temperature applications where metal balls would deform or fail.
### 3. Corrosion Resistance
Alumina ceramic balls demonstrate excellent resistance to most acids, alkalis, and organic solvents, ensuring reliable performance in corrosive environments.
### 4. Electrical Insulation
With high dielectric strength and volume resistivity, alumina ceramic balls serve as excellent electrical insulators in various electronic and electrical applications.
### 5. Low Density
Compared to steel balls, alumina ceramic balls are about 60% lighter, reducing energy consumption in rotating applications and minimizing bearing loads.
## Industrial Applications of Alumina Ceramic Balls
### 1. Bearings and Precision Components
Alumina ceramic balls are widely used in high-performance bearings for applications requiring:
– High-speed operation
– Corrosion resistance
– Electrical insulation
– Extreme temperature conditions
### 2. Grinding and Milling Media
In the pharmaceutical, paint, and ceramic industries, alumina balls serve as:
– Grinding media in ball mills
– Dispersion media for pigments
– Size reduction agents for powders
### 3. Valve Components
The chemical and petrochemical industries utilize alumina ceramic balls in:
– Check valves
– Control valves
– Metering pumps
where their corrosion resistance ensures long service life.
### 4. Semiconductor Manufacturing
In cleanroom environments, alumina ceramic balls are used for:
– Wafer handling
– Precision positioning
– Process equipment components
### 5. Aerospace and Defense
Critical applications include:
– Guidance systems
– Gyroscopes
– High-temperature bearings
– Radar components
## Manufacturing Process
The production of high-quality alumina ceramic balls involves several precise steps:
1. Powder preparation and mixing
2. Forming through isostatic pressing or extrusion
3. High-temperature sintering (1500-1700°C)
4. Precision grinding and polishing
5. Quality inspection and testing
## Quality Considerations
When selecting alumina ceramic balls, important factors include:
– Alumina content (90%, 95%, 99%, or 99.9%)
– Sphericity and surface finish
– Dimensional tolerances
– Density and porosity
– Mechanical strength
## Advantages Over Metal Balls
Alumina ceramic balls offer numerous benefits compared to traditional metal balls:
– Longer service life in abrasive environments
– Reduced maintenance requirements
– Energy savings due to lower mass
– Non-magnetic properties
– Better performance in corrosive media
– Higher operating temperatures
## Future Trends
The alumina ceramic ball market continues to evolve with:
– Development of nano-structured alumina for enhanced properties
– Improved manufacturing techniques for tighter tolerances
– Expansion into new industrial applications
– Growing demand in renewable energy technologies
As industries continue to push performance boundaries, alumina ceramic balls will remain a critical component in advanced engineering solutions across multiple sectors.