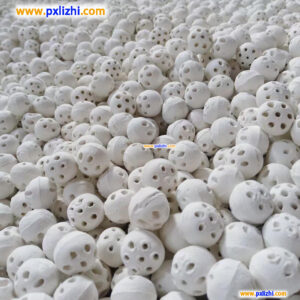
# Alumina Ceramic Ball: Properties and Applications
## Introduction to Alumina Ceramic Balls
Alumina ceramic balls are high-performance ceramic spheres made from aluminum oxide (Al₂O₃). These precision-engineered components have become essential in various industrial applications due to their exceptional mechanical, thermal, and chemical properties. With alumina content typically ranging from 90% to 99.9%, these ceramic balls offer superior performance compared to traditional metal or plastic alternatives.
## Key Properties of Alumina Ceramic Balls
### 1. Exceptional Hardness and Wear Resistance
Alumina ceramic balls boast a Mohs hardness of 9, second only to diamond. This extreme hardness makes them highly resistant to wear, even under continuous friction and high-load conditions. Their wear resistance is approximately 100 times greater than that of steel, ensuring long service life in abrasive environments.
### 2. Outstanding Thermal Stability
Keyword: alumina ceramic ball
These ceramic balls maintain their structural integrity at temperatures up to 1,600°C (2,912°F), with excellent thermal shock resistance. They exhibit minimal thermal expansion (coefficient of thermal expansion: 8.0×10⁻⁶/°C), making them ideal for applications involving rapid temperature changes.
### 3. Superior Chemical Inertness
Alumina ceramic balls demonstrate remarkable resistance to most acids, alkalis, and organic solvents. They are particularly resistant to:
– Hydrochloric acid (HCl)
– Sulfuric acid (H₂SO₄)
– Nitric acid (HNO₃)
– Sodium hydroxide (NaOH)
### 4. Electrical Insulation Properties
With high electrical resistivity (10¹⁴-10¹⁵ Ω·cm), alumina ceramic balls serve as excellent insulators, even at elevated temperatures. This property makes them valuable in electrical and electronic applications.
### 5. Low Density and High Strength
Despite their impressive mechanical strength (compressive strength: 2,000-4,000 MPa), alumina ceramic balls have a relatively low density (3.6-3.9 g/cm³), about half that of steel. This combination reduces centrifugal forces in rotating applications while maintaining durability.
## Common Applications of Alumina Ceramic Balls
### 1. Bearings and Precision Components
Alumina ceramic balls are widely used in:
– High-speed spindle bearings
– Dental handpiece bearings
– Semiconductor equipment bearings
– Aerospace components
Their non-magnetic properties make them particularly valuable in MRI machines and other sensitive medical equipment.
### 2. Grinding and Milling Media
In the industrial sector, alumina ceramic balls serve as:
– Grinding media in ball mills
– Dispersion media for paints and coatings
– Milling media for ceramics and minerals
– Polishing media for electronic components
### 3. Valve Components
The chemical resistance of alumina ceramic balls makes them ideal for:
– Chemical pump valves
– Metering valves
– Control valves in corrosive environments
– Oil and gas industry valves
### 4. Thermal and Electrical Applications
Specialized uses include:
– Insulators in high-temperature furnaces
– Heat-resistant spacers
– Electrical insulation components
– Semiconductor manufacturing equipment
### 5. Other Industrial Applications
Additional applications encompass:
– Textile guides and tensioners
– Flow control devices
– Pump components
– Wear-resistant liners
## Manufacturing Process Overview
Alumina ceramic balls are typically produced through:
1. Powder preparation (mixing and milling)
2. Forming (isostatic pressing or extrusion)
3. Sintering (high-temperature firing)
4. Precision grinding and polishing
5. Quality inspection and sorting
The manufacturing process can be adjusted to achieve specific properties by controlling:
– Alumina content (90%, 95%, 99%, or 99.9%)
– Grain size and microstructure
– Porosity levels
– Surface finish requirements
## Selection Considerations
When choosing alumina ceramic balls for specific applications